In this article, we’ll plunge further into underlay inside your weaving plans and digitizing while at the same time covering:
The significance and contrast of various underlay join
Involving underlay methods for convenient solutions
Underlay on caps and covers
Involving underlay in your product
Is it safe to say that you are new to weaving digitizing? Whether you’re hoping to make your own plans or basically better figure out what’s going on under your needle, remember to look at our Free Weaving Digitizing 101 video course! It even accompanies a cheat sheet pdf.
Understanding Underlay Lines in Weaving and Digitizing
Underlay lines are just running fastens put in specific spots, in specific headings, with shifting join lengths to give a weaving object (silk and fill lines) a strong groundwork.
Underlay texture and stabilizer model
Underlay additionally limits the chance of weaving puckering whenever it’s done sewing and out of the loop.
Underlay helps keep all your digitized protests clear cut, and it will make your top lines look all the more spotless and fresh. Underlay likewise permits you to develop layers of weaving on top of one another while diminishing the densities and keeping your plan clean by embroidery digitizing.
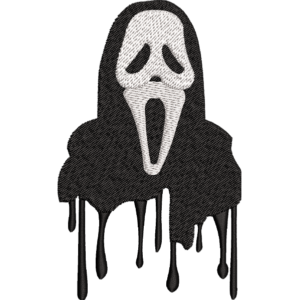
Why Are Underlay Lines So Significant In Weaving?
I will show you how underlay functions and why it’s crucial for know how to put underlay lines. We will show three basic section join utilizing a glossy silk line
Model 1: running line with underlay in the item.
Underlay down focus
In the model above, we’re utilizing a running join and putting several passes of underlay directly in the center of the item. What normally happens is that this glossy silk join will look somewhat spiked when it is sewed and will not have a fresh, clean look. I’m certain you’ve presumably taken a gander at a completed example that is fallen off your machine and asked why it doesn’t look perfect. It isn’t so much that your machine needs an update; this is on the grounds that the underlay was in some unacceptable spot.
Model 2: same section line with underlay put extremely near the edge of glossy silk fasten.
Underlay to near edge model
In the model above, we have a similar section join. In any case, this time, the underlay is set exceptionally near the edge of the silk join. This arrangement will have appalling outcomes as the underlay line might pop external the silk fasten, and afterward you need to meticulously choose that multitude of undesired strings.
Model 3: underlay is .4mm away from an external perspective of the article.
Underlay done appropriately model
In the model above, we place the underlay in a particular spot, precisely .4mm away from the external edge of the item. At the point when you run this example on your machine, you’ll see that the weaving lines out fresh and clean, with the underlay going about as a break wall.
Underlay Side View
The outline above shows a side perspective on what’s going on. The top string will pull towards the focal point of the segment, yet the underlay fasten will bring it to an abrupt halt so it won’t pull in any further of embroidery designs.

This helps while you’re sewing plans on inexactly woven texture types. Like the texture of a golf shirt, a woven texture would seem to be a progression of slopes and valleys from the side whenever set under a magnifying lens. On account of their temperament and how these textures are processed, they will generally extend more evenly than upward as articles of clothing are sewn/built as such. String could fall on one or the other side of a slope or valley regardless of whether it seems wonderful on your PC screen. Appropriately situated underlay will enormously diminish the probability of this sort of mutilation occurring.
You can lose a letter I in the crease of a cap, and in the event that you’re running a fill fasten on a level plane, the join can change in appearance when they go over the middle crease. We call it a join in the trench; the running line going all over a couple of times will fill in the middle crease, and the weaving will then, at that point, look compliment around there.
Whenever I’ve digitized the upward line, I’ll next begin to digitize a level fasten from the middle out (perhaps 10-15mm to one or the other side). Then, at that point, I’ll do the following pass 20-30mm, etc. Consider it moving to and fro, gradually streamlining the bended surface from the middle and in the long run stirring things up around town limits toward every path. This truly gives an establishment to plans that might not have been pathed to think about the bended surface of a cap.

I for the most part leave the underlay join I’ve quite recently made as a different variety change and afterward basically move it up in the sewing request, so it weaves first. On the off chance that you match the primary string tone as near the shade of the cap, it’s a decent defend. In the event that any of those fastens are uncovered after the plan is done weaving, they won’t be observable in light of the fact that the tones match.
Involving Underlay in Your Weaving Programming
Numerous product brands in the present market permit you to pick and control the kind of underlay and the properties allocated to the items you make. This is where I feel most embroiderers battle. It very well may be trying to realize which underlay to use for explicit fasten types, the width required in light of the articles being digitized, and the settings for all the fluctuating texture types accessible to sew on. Nonetheless, knowing all